Innovations creating customer value
We develop eco-efficient rock processing solutions in close collaboration with our customers, ensuring productive, sustainable and cost-effective crushing, screening, breaking and demolition solutions.
In 2024 we launched DeckMapp™, a digital platform for screen deck maintenance. The platform ensures that all tasks centered around screening media are managed within one seamless digital interface, providing customers with real-time data on laptop, tablet or mobile phone. The information provided enables smarter, data-driven decisions to optimize screening media maintenance.
An appreciated feature of the platform is the optional add-on WearApp™, an innovative wear assessment system powered by artificial intelligence (AI). Users simply capture images of worn screening media panels with a smartphone or a tablet. The system then applies AI to automatically assess each aperture, calculating amount of wear, panel efficiency and remaining wear life. The application makes substantial time savings and delivers far greater accuracy over traditional manual wear-assessment methods.

ACS-s is a series of energy-harvesting wireless sensors with magnetic mounts attached at strategic locations on the machine’s vibrating screen or feeder. These robust sensors are easy to install and do not require battery replacement. Customers have the option to either use their own teams to monitor alerts or leverage our global network of specialist engineers and maintenance teams to provide remote monitoring and situation response direction.
We upgraded the 800i crusher series with the ACS-c 5 automation system. The new role-based interaction functionality facilitates the work of operators, maintenance personnel, and engineers by offering guidance, access to valuable data, and tools for proactive maintenance and optimization – leading to productivity and uptime gains.
Screens, feeders and exciters are used in the harshest of mining environments and undergo a great deal of wear and tear. Our refurbishment program brings new life into aging mining equipment, offering a sustainable alternative to purchasing new machinery. By refurbishing and upgrading key components, the program not only extends the lifespan of equipment but also significantly reduces its environmental impact. This initiative supports the circular economy, cutting waste and minimizing the need for new raw materials.
Rock processing value chain (mining)
Our offering
- Crushing solutions
- Screening solutions
- Mobile crushing and screening
- Hydraulic breakers, booms and demolition tools
- Parts, services and consumables
- Digital services and solutions
Examples of innovations
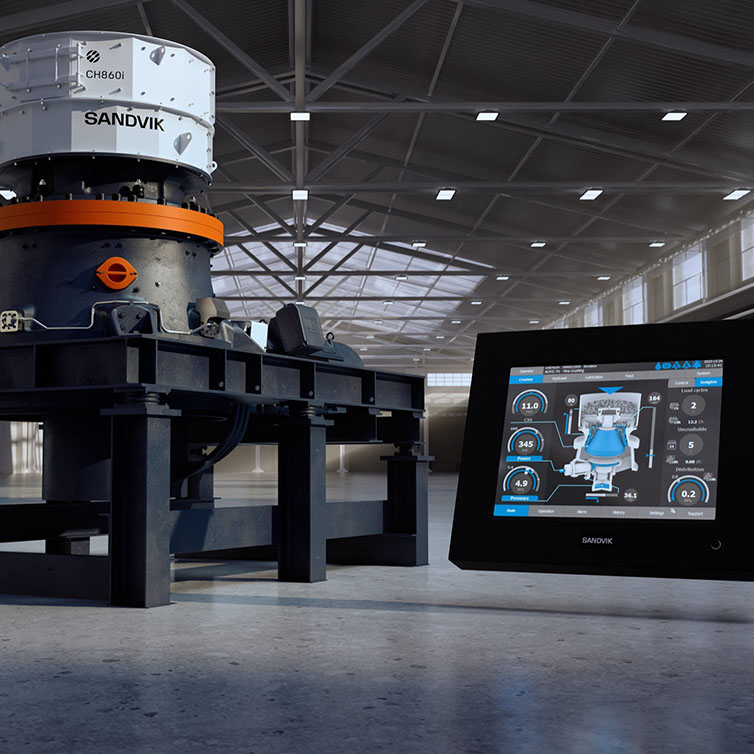
The 800i crusher series was upgraded with the ACS-c 5 automation system. The new solution facilitates the work of operators, maintenance personnel, and engineers by offering guidance, access to valuable data, and tools for proactive maintenance and optimization – leading to productivity and uptime gains.
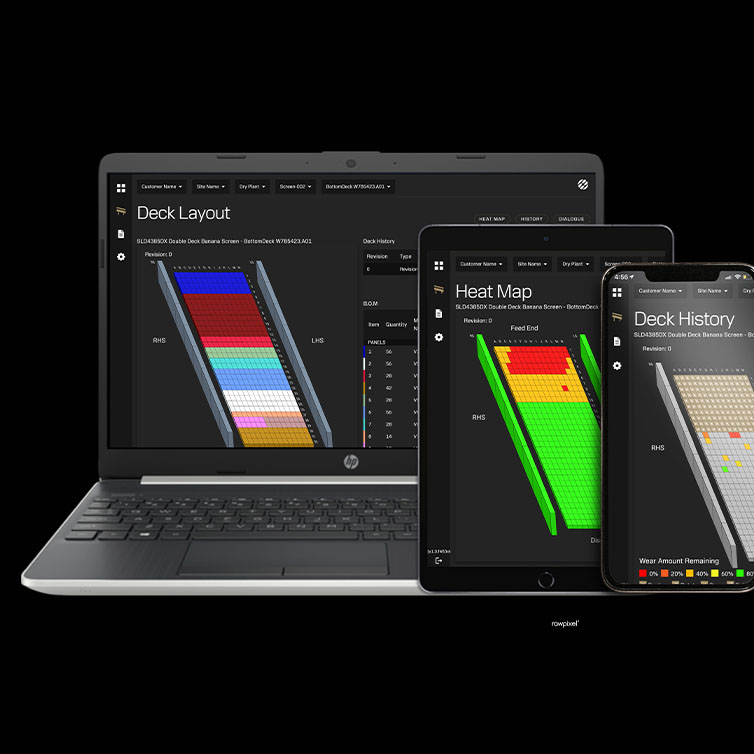
We launched DeckMapp™, a digital platform for screen deck maintenance. The platform provides customers with real-time data on laptop, tablet or mobile phone and the information provided enables smarter, data-driven maintenance decisions to optimize screening media strategy. An optional add-on is WearApp™, a wear assessment system powered by artificial intelligence (AI). The system applies AI to automatically assess and calculate the amount of wear, panel efficiency and remaining wear life. The application makes substantial time savings and delivers far greater accuracy over traditional manual wear-assessment methods.
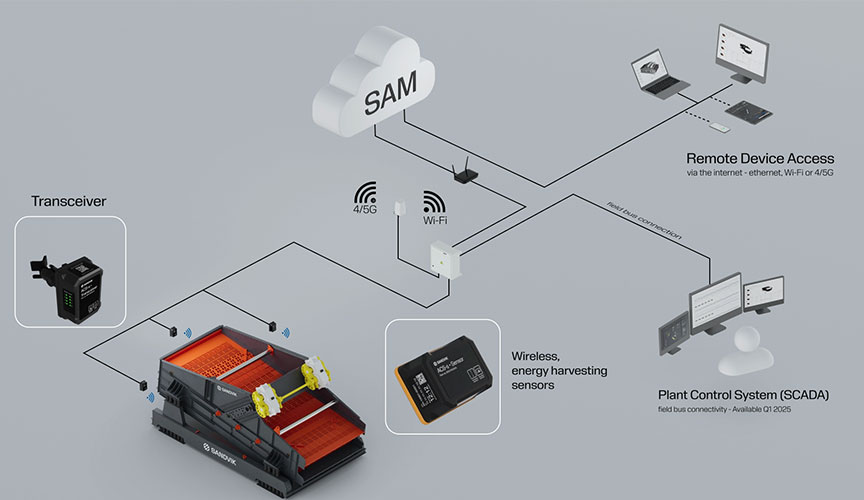
We launched ACS-s, a series of energy-harvesting wireless sensors connected with the digital platform SAM® and attached at strategic locations on the machine’s vibrating screen or feeder. The system provides operators and service technicians with real-time, easily comprehensible data on the condition of their equipment, enabling proactive maintenance decisions.