Health and Safety
Sandvik is working steadily towards its vision of Zero Harm through the implementation and continual improvement of Environment, Health and Safety management systems. This is coupled with a wide range of activities to improve the already strong health and safety culture.
Our vision is Zero Harm to our people, our customers, our suppliers and the environment we work in. A strong health and safety culture with a “people caring for people” mindset is helping us to achive this. The last time the question was asked in our employee survey, 88 percent of respondents rated the safety culture at Sandvik as either “strong” or “very strong.”
This health and safety culture permeates the whole company, and it starts from the top, with Environment, Health and Safety (EHS) leadership being one of the focus areas for the Sandvik EHS Objectives. This is implemented in Sandvik Mining and Rock Technology, for example, by leaders committing to three personal EHS leadership behaviors that are then monitored and measured. By “walking the talk” the leadership team is turning “wanted behaviors” into measurable processes and then into leading indicators that can tell a story that inspires positive cultural change.
Metrics drive culture
We believe that what gets measured gets done. Sandvik’s EHS management systems and tools provide a structured approach to setting, implementing and monitoring our health and safety targets. The Sandvik EHS Council consists of representatives from each business area with its primary aim being to facilitate collaboration across the company that will enhance our progress towards our EHS vision.
Our EHS management systems are audited by external agencies to ensure that they meet internationally accepted standards (OHSAS 18001 or equivalent) and are regularly audited internally to continually improve our operating practices. Every non-administrative Sandvik location with more than 25 people is required to have external certification within two years of commencement or acquisition. Currently all of these locations meet this requirement, with the exception of one site where the process has been delayed.
Sandvik’s EHS Policy and Group EHS Objectives drive our health and safety activities. Each business area works to meet these objectives according to their own plans, but with the common aim of eliminating all work-related fatalities and minimizing the number of work-related injuries and illnesses. Targets are set year on year to drive performance on all organizational levels. For more health and safety-related data, see Sustainability notes - Key figures.
Performance in 2018
Sandvik’s health and safety work shall comply with all relevant legislation and we strive to go beyond compliance to ensure the best performance for both our employees and our customers. We utilize a wide range of leading and lagging indicators to measure safety and health performance in every Sandvik location, including Lost Time Injury Frequency Rate (LTIFR) and Total Recordable Injury Frequency Rate (TRIFR). Both of these indicators show long-term positive trends. In 2018, the LTIFR (LTIs per million hours worked) increased to 1.7 (1.6), mainly driven by an increased number of low level LTIs (1-2 days lost) within Sandvik Materials Technology. However, the business area reduced its TRIFR by 24 percent which contributed to the Group TRIFR being reduced to 4.0 (4.6). As the LTIFR gets to lower levels, Sandvik is moving towards a greater focus on TRIFR as its primary safety performance indicator. There have been no fatalities to report since 2015.
Using a Significant Incident Alert process, business areas can quickly inform other parts of the organization of incidents that are relevant across the company to minimize the likelihood of a recurrence.
TRIFR by Business area
TRIFR and LTIFR
LTIFR by Business area
Development of different injuries included in TRIFR and LTIFR over time. An LTI is an accident resulting in time away from work, a RWI (Restricted Work Injury) is an injury where you can be at work but you can’t perform your ordinary work, and a MTI (Medical Treatment Injury) is when you need some kind of medical treatment but can perform your normal work.
Employee well-being
In line with the United Nations Sustainable Development Goals, we aim to have a culture and working environment that supports the good health and well-being of our employees. All of our sites should offer health and well-being programs that have been adapted to local needs. The programs address a wide range of issues such as fitness, nutrition, mental health and disease prevention.
Occupational illness
The increasing incidence of work-related mental health issues is a concern for many communities around the world. To address this concern, Sandvik launched company campaigns in 2018 to increase awareness and education for employees about mental health issues, for example Australia’s “R U OK?” (Are you OK?) campaign. Sandvik has processes in place to record and investigate occupational illnesses to determine the root causes and develop prevention strategies.
Hazardous materials
Within production we continually work to replace hazardous materials with less hazardous options or, where replacement is not an option, minimize the use of hazardous materials. We are also investing in new equipment and in improving our processes to reduce employee exposure to hazards such as noise, dust and exposure to gases or other substances. Our products and solutions are designed to help our customers improve their health and safety as well, for example by reducing their exposure to chemical hazards. Our battery-driven underground mining equipment helps to alleviate the potential health impacts of diesel particulate matter and other engine emissions.
Safety forums
Sandvik is the only Original Equipment Manufacturer (OEM) on the Mining Safety Round Table (MSRT), formed by Sandvik and other major mining companies to share and learn from operational practices with the aim of preventing workplace fatalities. Sandvik is also a member of the Earth Moving Equipment Safety Round Table (EMESRT) and the International Council on Mining and Metal’s (ICMM) innovation forum for cleaner, safer vehicles. These collaborative forums aim to encourage and facilitate improvements to eliminate mining equipment-related fatalities, improve underground air quality and reduce emissions of greenhouse gases.
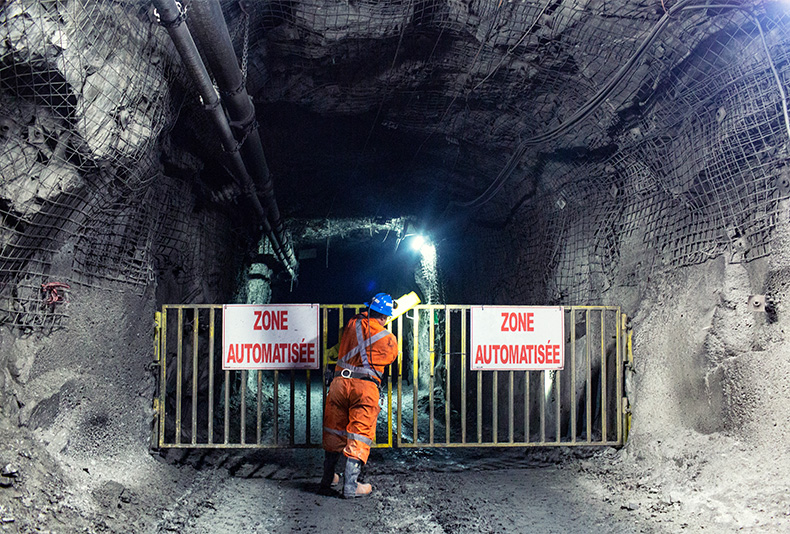
Automating mining equipment reduces the risks for employees, who can work above ground while mining equipment is maneuvered into riskier and difficult-to-access locations.