Portable tubing solution supports hydrogen fuel expansion
Our onsite tubing solution is making the delivery of hydrogen safer and more efficient for long-time customer Linde.
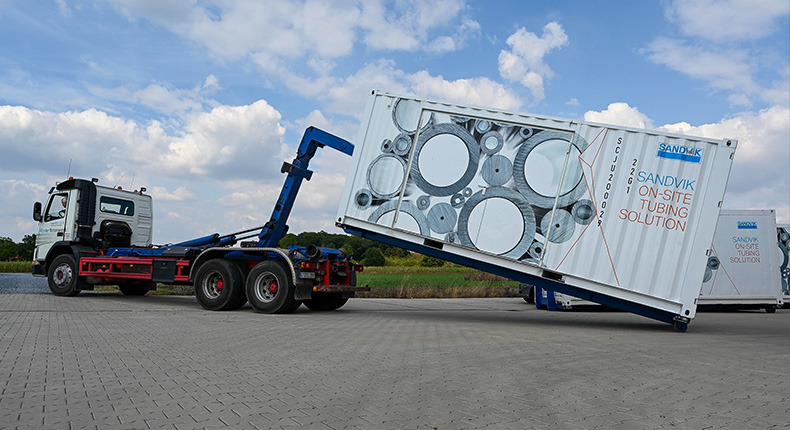
Sandvik is playing an important role in Linde’s expansion of hydrogen-fueling stations by supplying the company with tube solutions on site through a digitally connected Sandvik Mobile Service Solutions container.
Linde is a leading industrial gases and engineering company with customers in more than 100 countries. The company has more than 20 years of experience in hydrogen mobility applications, among its activities, and in recent years has been building hydrogen stations to fuel vehicles.
As a renewable element, hydrogen (H₂) plays a fundamental role in achieving sustainability targets by providing an alternative to fossil fuels. And, as demand for greener vehicles grows, so does the need for hydrogen to power such vehicles.
Linde has built more than 160 hydrogen-fueling stations at commercial filling stations in more than 15 countries to date, and further stations are underway. Sandvik is playing an important role in Linde’s expansion by supplying the company with tube solutions on site through a digitally connected Sandvik Mobile Service Solutions container. The stainless steel alloy tubes are used to transport hydrogen from a storage tank to a dispenser usually located about 40-60 meters apart.
Made to measure
Sandvik personnel arrive with the container at the station. At the station, the 150-170 meter coiled tubing is straightened through our patented technology and cut to match Linde’s exact specifications at each location.
“Installations on customer sites differ from project to project so it is essential to have tube solutions which allow us to realize different dimensions and lengths to connect the necessary units on the fueling station site,” explains Johannes Fritzer, Research and Development, Linde Hydrogen FuelTech.
This convenient solution is both sustainable and cost-efficient as it eliminates waste by cutting only as much as is required, and eliminates the need for customers to keep large coils in stock. Sandvik’s corrosion-resistant tubing solution also offers the highest possible level of safety.
Safety a priority
“It is essential regarding safety aspects that the tubes meet certain quality requirements which are taken into account for the pressure rating of the different ranges in use,” says Fritzer. Linde’s hydrogen gas is transported under both low and high pressures of up to 900 bars and the high-quality tubes from Sandvik meet the strict safety guidelines for hydrogen transportation.
Our long tubing also reduces the risk of accidents by eliminating the need for conventional fittings such as cone and thread connections or welding, which are normally used to connect shorter tubes. Eliminating connections helps reduce the risk of leakage and station shut downs, increasing safety for both the site and the surrounding neighborhood. The lack of connections also makes the burying of hydrogen transporting tubes feasible.
Johannes Fritzer highlights yet another benefit with the convenient container solution: “From a logistical point of view the Sandvik solution eases the planning of the construction site through an unproblematic direct delivery of the needed tubes, with no ordering, storage or other logistical issues,” he says, adding that he is pleased with Sandvik Mobile Service Solutions thus far.
“Overall there has been a very positive response from all parties involved in the process. Sandvik has good customer service, is technically professional and provides a consistently outcome-oriented approach. We will certainly continue to rely on Sandvik’s support.”